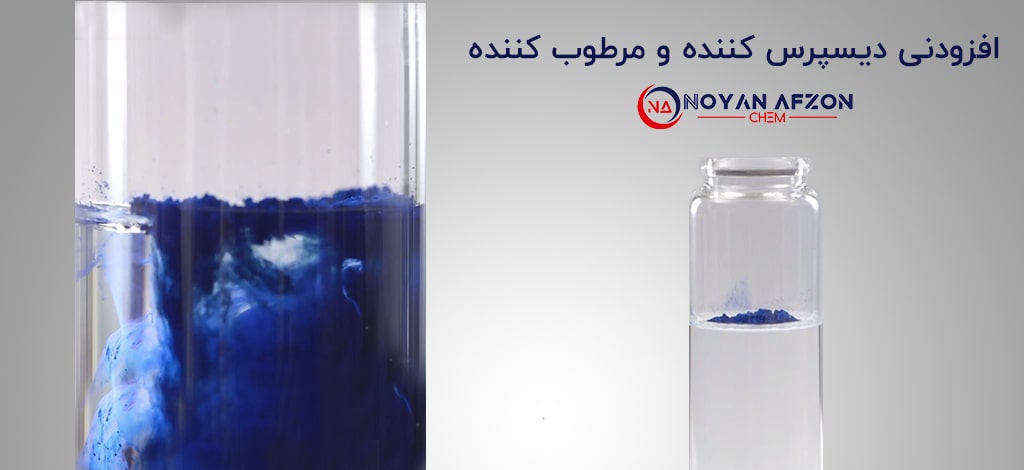
چرا باید در رنگ از دیسپرس کننده استفاده کنیم؟
دیسپرس شدن (پخش شدن) و تثبیت بهینه ذرات پیگمنت (رنگدانه) عامل مهمی در تعیین خصوصیات نهایی رنگ، لاک و یا جوهر چاپ (مرکب چاپ) می باشد که از جمله آنها می توان به ویسکوزیته، دانه بندی، پایداری در زمان انبارداری و …اشاره نمود. رنگدانه ها و مواد پرکننده فرمول باید توسط آسیاب به صورت ذرات ریز با اندازه ذرات مناسب درآمده، مرطوب و تا حد ممکن به صورت پایدار پخش گردند. فقط در این صورت است که می توان میزان شدت رنگ، براقیت، قدرت پوشانندگی، مقاومت در برابر نور و هوا را در پوشش به حداکثر میزان خود رساند. در صورتی که مرحله دیسپرسیون (توزیع یکنواخت) به خوبی انجام نشود، طیف گسترده ای از نقایص در رنگ و پوشش رخ خواهد داد که از جمله آنها میتوان به:
- لخته شدن، ذرات رنگدانه های مجزا با هم جمع می شوند و ساختارهای بزرگتری ایجاد می کنند که با افزایش ویسکوزیته همراه است،
- كاهش براقيت رنگ به دلیل تشکیل ذرات رنگدانه بزرگتر (لخته شده)،
- رسوب و ته نشینی پیگمنت، برای ذرات رنگدانه بزرگتر (لخته شده) تشکیل رسوب راحت تر است که خود در تغییر ظاهر رنگ و فام موثر است،
- تغيير فام، عدم تکرار پذیری و یکنواختی فام رنگ در مقایسه با فام دلخواه
- فلوتاسيون (رو افتادگي یا شناور شدن)، موثر در ظاهر رنگ و فام
- عیوب ظاهری به دلیل تجمع ذرات (نقطه نقطه شدن فیلم رنگ)
- سلولهاي بنارد (Bénard)
- لولینگ یا همترازی ضعیف
- شره رنگ، تاثیر منفی در خواص رئولوژیک رنگ
- رگه رگه شدن پیگمنت در سطح فیلم نهایی
- کاهش قدرت پوشانندگی.
فرآیند پراکندگی و دیسپرس شدن رنگدانه ها
ایجاد دیسپرسیون و تثبیت رنگدانه ها، در پروسه ی ساخت رنگ، از نظر صرف زمان و انرژی، جزو پردردسر ترین مراحل به شمار می آید و بدون افزودنی های مرطوب کننده و دیسپرس کننده مناسب به سختی امکان پذیر می باشد. فرآیند پراکندگی و دیسپرس شدن رنگدانه ها را می توان به سه مرحله کلی تقسیم نمود (که بخشی از این مراحل به طور متوالی و تا حدی همزمان رخ می دهد) که شامل:
- مرطوب شدن (خیس شدن)، جایگزینی هوا و آب با رزین (محمل یا بایندر)،
- آسیاب مکانیکی، شکسته و جدا شدن ذرات و کاهش دانه بندی، رسیدن به اندازه ی اولیه،
- دیسپرس شدن (پراکندگی)، توزیع ذرات در مایع،
- تثبیت، حفظ جدا ماندن ذرات برای مدت طولانی.
در ادامه به طور مفصل در مورد هر یک از این فرآیندها توضیح داده خواهد شد.
فرآیند آسیاب کردن رنگدانه
در طی مرحله آسیاب رنگدانه ها، اندازه دانه های رنگدانه (آگلومرها) کاهش می یابد و ذرات اولیه تهیه می شود. آگلومرها (Agglomerate) همان اجتماع ذرات در پودر هستند و فضای بین ذرات رنگدانه منفرد از هوا و رطوبت پر شده است. این ذرات رنگدانه ای منفرد فقط در امتداد لبه ها و گوشه های خود با یکدیگر در تماس هستند. نیروهای تعاملی بین ذرات آگلومره نسبتاً کم هستند و می توان با استفاده از تجهیزات دیسپرس کننده معمولی بر چنین نیروهایی غلبه نمود. این مرحله با اعمال انرژی مکانیکی انجام میشود. در عمل این کار با میکسر (mixer) و با سرعت بسیار بالا قابل انجام است. ایجاد دانه های کوچکتر منجر به افزایش سطح مرزی بیشتر با محیط مایع می شود. در طی این فرآیند، انرژی به سیستم داده می شود و بنابراین ذرات کوچکتر با سطح تماس بزرگتر با محلول رزین (محمل یا بایندر) تشکیل می شود. سپس سیستم تلاش می کند تا از این حالت غنی از انرژی فرار کرده تا به حالت کم انرژی قبلی خود بازگردد. رنگدانه های ریز توزیع شده دوباره به هم می رسند و ساختارهای بزرگتری را تشکیل می دهند که به عنوان لخته یا همان فلوکوله شناخته می شوند که با کاهش قدرت رنگ، کاهش براقیت و تغییر رئولوژی در رنگ همراه است.
فرآیندهای مختلفی که در طی آسیاب کردن رنگدانه ها رخ می دهد را می توان به سه مرحله زیر تقسیم کرد:
- مرحله 1، تر کردن (مرطوب یا خیس کردن): تمام هوا و رطوبت موجود در سطح رنگدانه با محلول رزین (بایندر یا محمل) جایگزین می شود و محلول رزین باید به فضای بین آگلومرها نفوذ کند. محلول رزین (بایندر یا محمل) ذرات رنگدانه را تر (مرطوب، خیس) می کند و رابط جامد/گازی (رنگدانه/هوا) به یک رابط جامد/مایع (محلول رنگدانه/بایندر) تبدیل می شود. برای انجام این کار، محلول رزین باید به فضاهای بینابینی آگلومرها نفوذ کند.
- مرحله 2، دیسپرس کردن: مرحله آسیاب رنگدانه ها که نشان دهنده پراکندگی واقعی رنگدانه است. از طریق انرژی مکانیکی (نیروهای ضربه و برشی)، پیگمنت های آگلومره شکسته می شوند و اندازه آنها کاهش می یابد.
- مرحله 3، تثبیت کردن: جداسازی خوب ذرات در محیط رنگ مایع به تنهایی جهت اطمینان از پراکندگی و دیسپرسیون خوب ذرات در فیلم خشک کافی نیست و ذرات پیگمنت باید در بهینه ترین حالت دیسپرسیون در طی فرآیند تولید، انبارداری و اجرا و حتی در حین خشک شدن رنگ قرار گیرند. پراکندگی و دیسپرسیون رنگدانه باید به منظور جلوگیری از تشکیل فلوکوله یا همان لختگی کنترل نشده و ناخواسته تثبیت شود. با تکنیک های خاص، می توان ذرات رنگدانه را در فواصل مناسب از یکدیگر نگه داشت تا تماس مجدد نداشته باشند.
مراحل 1 (تر کردن) و 3 (تثبیت کردن) می تواند تحت تأثیر مواد افزودنی باشد. مواد افزودنی تر کننده (مرطوب و خیس کننده) باعث تسریع در تر شدن ترکیبات رنگدانه توسط رزین می شوند. مواد افزودنی دیسپرس کننده باعث تثبیت پراکندگی و دیسپرسیون رنگدانه ها می شوند. یک محصول مشابه می تواند اغلب هم به عنوان ماده افزودنی مرطوب کننده و هم دیسپرس کننده عمل کند.
مواد افزودنی به مرحله 2، مرحله آسیاب رنگدانه ها کمک نمی کنند. در اینجا مهم است که نیروهای مکانیکی به اندازه کافی بزرگ باشند تا آگلومرها را از هم بپاشند و زمان بهم پیوستن آگلومرها در حوزه عملکرد این نیروها به اندازه کافی طولانی باشد. اگر تا آنجا که ممکن است آگلومرها از هم جدا شوند، افزودنی های دیسپرس کننده می توانند این حالت را تثبیت کرده و لخته سازی را به طور موثر سرکوب کنند.
يكي از پديدههاي مهـمی كـه كشـش سـطحي بـر آن اثـر گـذار اسـت، ترشوندگي است. به طوری كـه هـر چه كشش سطحي مايع بيشتر باشد، قطرات مايع، تمايل بيشـتري بـه داشـتن شـكل كـروي روي سطح جامد داشته و خود مايع تمايل به كمتر شدن برهمكنش بين آن مايع و جامد دارد. به عبارتي هر چه كشش سطحي مايع بيشتر باشد، مايع، سطح زيرلايه را كـمتـر خيس ميكند و زاويه تماس بيشتري دارد.
نویان افزون شیمی به عنوان تنها تولید کننده تخصصی افزودنی دیسپرس کننده تر کننده برای جلوگیری از فلوتاسیون.
با کدهای NACO-DS 1014 ،NACO-DS1060 ،NACO-DS1022 ،NACO-DS 1065 ،NACO-DS1013 برای تمام رنگ ها و پوشش ها بر پایه حلال، از شما بابت صرف وقت جهت مطالعه این مقاله تشکر مینماید.
اگر میخواهید با مکانیسم دیسپرسیون بیشترآشنا شوید کلیک کنید!
برای معرفی انواع دیسپرس کننده های پلیمری کلیک کنید!
برای آشنایی با تاثیر فلکولیشن (لخته سازی) کنترل شده در دیسپرسیون پیگمنت کلیک کنید!
برای آشنایی با فلوتینگ رنگ کلیک کنید!
برای آشنایی با خمیر رنگدانه ها کلیک کنید!
برای توصیه های کلیدی در مورد نحوه استفاده از دیسپرس کننده ها در رنگ کلیک کنید!
برگرفته از وبسایت BYK آلمان